信州 時の匠工房 研磨師 黒木 友志
ゆがみのない平面を生み出す
下地処理、ザラツ研磨とは
「ザラツ研磨」は副資材(信州 時の匠工房ではサンドペーパー)を貼った円形の定盤を回転させ、そこにケースを当てて面をならし、角を整えるための下地処理技術です。かつて存在したスイスの工作機械メーカー「SALLAZ」がその名の由来とされています。
ザラツ研磨によって平面の歪みをなくし、平面と斜面の繋ぎ目のエッジを際立たせたシャープなケースを仕上げる技術は、熟練の腕と豊富な経験を要するため、その難易度の高さから海外の高級時計では殆ど見られなくなりました。しかし卓越した技能を継承し続ける信州 時の匠工房では、僅かな光も拾って輝く美しいケース仕上げに不可欠なこの研磨技術を、今もなお採用しています。20以上もある研磨工程の中でも、特に精緻な職人技が求められるザラツ研磨。
ケースの形状や上下左右のバランスを崩さないよう細心の注意を払いながら、ケースを当てる力加減と手を動かすスピードだけで、目視と感覚値を頼りに仕上げていきます。
信州 時の匠工房ではチタンやステンレススチール素材だけでなく、柔らかく加工の難しい18Kゴールドやプラチナケースのザラツ研磨も手掛けています。グランドセイコーの18Kゴールドケースを手掛けることのできる研磨師は、信州 時の匠工房の中でも僅か数名。プラチナケースにいたってはただ一人です。まさにグランドセイコーが世界に誇る技術です。
信州 時の匠工房 研磨師
黒木 友志
2001年、セイコーエプソンに入社。それまでの工程別に研磨作業を行っていた分業体制から、現在の1人が複数工程を担当する一貫体制へと移行した時期であり、 複数の先輩方から研磨技術を学んだ5年間の修行を含む15年が経過した現在では高い技術レベルに到達。入社以来、研磨一筋で培ってきた経験と高い技能から、若くして高級品を任されるようになりました。グランドセイコーならではの平面と稜線が際立つシャープな造形は、職人の僅かな狂いも見逃さない鋭い目と、寸分の違いも許さない研磨技術によって生み出されています。 限界を作らず常に次なる高みを目指す自分でありたい、という黒木の信念が2016年新たな研磨技術を生み、不可能とされていたプラチナ素材のシャープなケース仕上げを可能にしました。
「美しさ」を生み出す職人技 信州 時の匠工房 研磨師 黒木 友志 インタビュー
ケース素材によって研磨に要する時間が大きく異なるのですね。
「ステンレススチール」の研磨を基本とすると、「チタン」はステンレススチールに比べて一度熱がかかると肌荒れ(表面がボコボコした状態)を起こしてしまい、完成品にはなりません。そのため研磨熱ができる限りかからないよう、定盤の回転速度を落としたり、時間をかけて少しずつ削ったりすることで、綺麗な面に仕上げていく必要があります。
「18Kゴールド」は柔らかい素材なので、ステンレスと同じ研磨を行うと余分に削れてしまったり、角が取れケース全体が丸みを帯びた形状になってしまいます。シャープなエッジを非常に出し難い素材なんです。18Kゴールドを好まれるお客様は、金独特の優しいフォルムが好きな方も多くいらっしゃるので、あえて丸みを帯びたデザインに仕上げることもありますが、グランドセイコーの特徴でもある、平面を主体としたケースを崩さないように研磨するためにはチタン同様、定盤の回転速度と力加減を慎重に調整しながら作業しなければなりません。
「プラチナ」は最も扱いが難しく、基本的にはステンレススチールと同じ加工が不可能な素材です。ステンレススチールと同じ研磨方法では、ピンホール(白いブツブツ)が沢山できてしまうからです。それを取りに行くと、エッジがなくなりケースに丸みが出てしまいます。一般的にプラチナケースに丸いデザインが多いのはこのためです。シャープ感を出すことが非常に難しい素材なんです。そのためプラチナの研磨に使う副資材は専用のものを使用していますし、作業工程も格段に多く、一工程にかける時間自体も長くなるため、非常に手間がかかります。
グランドセイコーには“セイコースタイル”をもとに守り続けているデザイン方針*がありますよね。SBGD001はなぜプラチナ素材でシャープなエッジを出すことができたのでしょうか?
*グランドセイコーのデザイン方針
1)平面を主体として、平面と二次曲面からなるデザイン。三次曲面は原則として採り入れない。
2)ケース・ダイヤル・針のすべてにわたって極力平面部の面積を多くする。
3)各面は原則として鏡面とし、その鏡面からは極力歪みをなくす。
セイコースタイルをもつグランドセイコーのケースをプラチナで作りたいというお話を貰った時「基本的にはできない」と思いました。それでもデザイン側の要望を何とか叶えられないものかと、プラチナの素材特性を研究することから始めてみたところ、プラチナは硬度的にもステンレススチールより柔らかく、粘っこい性質を持っていることが分かりました。素材特有の性質を消すことはできないため、柔らかく粘っこい性質を持つ素材でいかにフラットな鏡面を出すかという点に絞って研究を重ねました。
注目したのは研磨剤と素材との関係性です。
研磨するサンドペーパーには砥粒が吹きつけられているのですが、ステンレススチールは、ケース表面の小さな凹みに粒子が入り込み難く、また入っても取り除きやすい。 一方、柔らかくて粘り気のあるプラチナは、ケース表面の凹みに粒子が入り込みやすく、一度入るとなかなか取れないし、入り込んだ粒子が脱落するとそこに穴が空いてしまう。穴が空いた状態を、バフ加工を施して平滑面に直そうとしても、粘り気のある特性から穴が横に伸びてしまい簡単には消せない。この点に気づいたんです。
ではプラチナ特有の表面の凹みをどうやってなくしたのですか?
表面をできるだけ細かい目に仕上げていくことで、ブツブツとした凹みを小さくしていく。凹みが小さければ、バフを沢山かけなくてもツヤになる、ということが分かってきました。
そこでザラツ研磨に使用する副資材と作業工程を、大幅に変えてみました。 凹みを小さくするためには細かい目のサンドペーパーをかければ良いのですが、いきなり細かい目で研磨しても綺麗な鏡面にはなりません。目の粗いものから徐々に細かいものへと何段階も踏んで少しずつ凹みの小さい面に仕上げていく。この方法にやっと辿り着きました。
開発にはどのくらいの時間がかかりましたか?
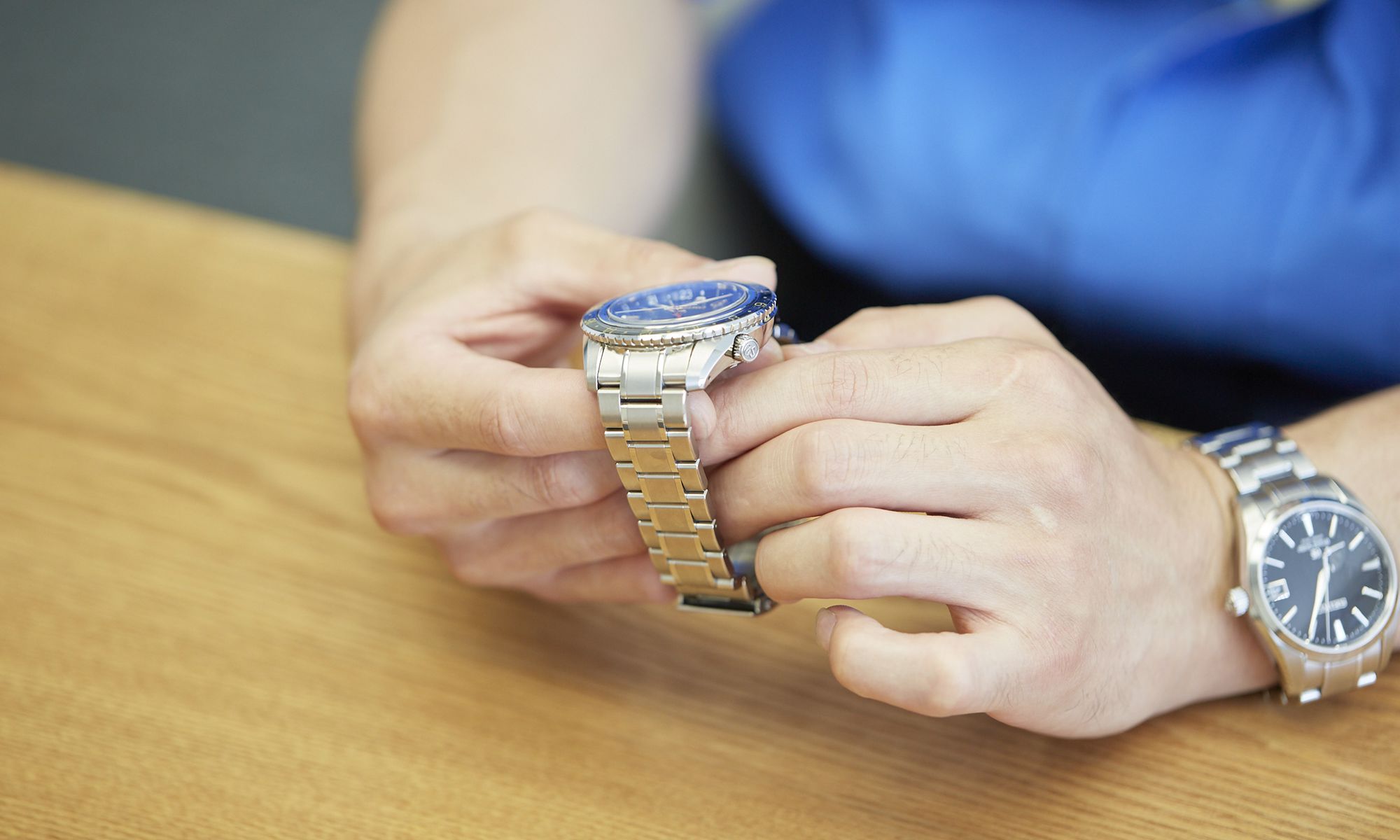
黒木さんにとってベストな仕上がりとは?
時計はジュエリーと同じ宝飾品でもあって、雑な仕上げであってはならないと思うんです。研磨は図面とケースサンプルを見ながら、寸分違わないものを作り続ける作業なので、図面やサンプルと全く同じ形状に仕上がることが、研磨工程におけるベストな仕上がりだと思います。加えてアールの部分がいかに凹凸なく美しく仕上がっているか、平面がいかに歪みのない綺麗な状態で仕上がっているか、そこまでできて初めて合格です。
自分のやった仕事が、お客様に喜んで頂く完全なものを作り込みたい、もっと良くしたいという思いが強いですね。
研磨工程のほとんどを手作業で行われているのですね。
機械で作る場合、一台で最初から最後までの全工程を行える機械はないので、工程ごとにケースを機械に乗せ替えることになると思いますが、乗せ替えを行うと僅かな誤差が生じるんです。1ミクロンでも誤差が出ると面は崩れてしまいます。 でも手作業であれば、目で見ながら研磨していく中で、その1ミクロンの誤差を仕上げることができます。もし切削工程から上がってきたケースで、4つのかんの形状が多少ずれていたとしても、人の手で加工すれば僅かな狂いを全て整えることができる。そこがどんなに技術が発達しても、人の手が外せない理由なのかなと思います。
1ミクロンの誤差を人の目と手は調整できるとは、すごいですね。幼少の頃から手先が器用だったのですか?
壊れた家電製品、中でも小さいものを分解するのが好きでした。プラモデルもよく作っていましたね。器用だと言われることもありましたが、器用な人ってそれなりに努力しているんじゃないかと思います。僕の場合、どうすれば同じ仕上がりのものを100個作れるか、どうすれば今よりも高い品質に仕上げられるか、ということを常に考えて仕事しています。そこを突き詰められる人の方が、すごくいい物を作れるんじゃないかと思うんです。
努力している人は「あの人すごい人ですね」と一目置かれるような人になると思います。私自身、そういう人に憧れ、そういう人になりたいと思い仕事をさせて頂いています。
お客様が手に取られた時、どんな風に感じて頂けると嬉しいですか?
「この腕時計をつくった人は誰ですか?ケースを磨いている人は誰ですか?」という答えを言って頂きたいですね。
「この腕時計をつくった人は、この方です。」と紹介されてお客様が気に入ってくださるのも嬉しいですが、やはり手に取っていただいたお客様の方から「この腕時計を磨いた人は誰ですか?作った方に会わせて貰えませんか?」というような言葉を頂けたら、作り手としてはとても嬉しいです。