-
日本初の腕時計
ローレル“腕時計の時代”の到来をいち早く見据え開発した、12型(直径約26.65mm)の日本初の腕時計。当時、日本の時計産業において冒険的な挑戦であり、画期的な発明となったセイコー初の腕時計「ローレル」の商品化以降、設計技術・微細加工技術や工作機械開発が大きく進化していくことになる。
-
セイコー初の紳士用
中3針モデル スーパーセイコーの腕時計で初めて、6時位置の小秒針ではなく、時分針と同じくセンターに秒針を配置した、紳士用の中三針モデル。既存設計を応用した伝え車方式ではなく、一から設計し直すことでセンター秒針を実現。このモデルの出現により、日本に本格的な中三針腕時計の時代が到来。
-
セイコー初の独自設計
マーベル狂わない、壊れない、美しいという腕時計の原理原則に立ち返り、セイコーが初めて独自設計した、当時、最高の精度を誇る紳士用機械式時計。新しい設計方針と生産技術設備の導入により開発されたこのモデルは、技術的革新をもたらすとともに、ジャパンメイドの腕時計のイメージを一変させる新時代への礎となった。
-
更なる高精度化を図った
当時の最上位機種 ロードマーベルマーベルの後継機種として、実用重視の設計思想から高精度化を図った、当時のセイコーの最上位機種。ムーブメントにも鏡面仕上げを施し、角穴車などを彫り込み、ねじには磨きがかけられるなど、普段見えない細かい部分にもこだわりの意匠が凝らされている。
-
高精度な大型ムーブメントを搭載
クラウン1956年発売のマーベルをベースに、さらなる高精度化を目指して開発された大型ムーブメント、キャリバー560を搭載したモデル。12mm径の大型てん輪を採用し、てんぷ性能も向上させ、ぜんまいを格納する香箱も大型化してトルクを高めた。
ムーブメント設計 平野 圭
外装設計 石田 正浩
メイド・イン・ジャパン
機械式腕時計の歴史
1881年の創業以来、絶え間なく進化を続けてきたセイコー。1913年に発売した国産初の腕時計「ローレル」を皮切りに、さらなる高精度化、高品質化を目指して、次々と技術革新を図り、今もなおその魅力が語り継がれるメイド・イン・ジャパンの機械式腕時計を生み出してきた。
既存設計を応用した伝え車方式に代わって、一から設計し直すことでセンター秒針を実現させたセイコー初の紳士用の中三針モデル「スーパー」(1950年)。“狂わない、壊れない、美しい”という腕時計の原理原則に立ち返り、セイコーが初めて独自設計を手掛けた、最高の精度を誇る紳士用機械式時計「マーベル」(1956年)。日本産腕時計のイメージを一変させたこの画期的なモデルの後継機種であり、実用重視の設計思想から高精度化を図った、当時のセイコーの最上位機種でもある「ロードマーベル」(1958年)。マーベルをベースとし、さらなる高精度化を目指して開発された大型ムーブメント、キャリバー560を搭載した「クラウン」(1959年)。こういったエポックメイキングな発明の数々は、現在に続くジャパンメイドの機械式腕時計の礎を築き、日本の機械式腕時計の発展に大きく貢献している。
機械式ウオッチブランド
「セイコー プレザージュ」とは?
100有余年に渡るセイコーの機械式腕時計づくりの伝統とノウハウを受け継ぎ、メイド・イン・ジャパンの機械式腕時計を生み出すウオッチブランド「セイコー プレザージュ」。禅の庭をモチーフにしたモデルや、琺瑯、七宝を駆使したモデルなど、日本独自の伝統技術、日本人の美意識と豊かな精神性を随所に盛り込みながら、伝統とテクノロジーが融合した幅広い商品ラインアップは、2016年から本格的にグローバル展開をスタートし、世界中で高い評価を得ている。
ムーブメント設計
平野 圭
2001年盛岡セイコー工業株式会社入社。同年セイコーインスツル株式会社(SII)へ出向。ムーブメント事業部 時計設計部 設計一グループにおいて、グランドセイコー メカニカルキャリバー9S6系やアナログクオーツ クロノグラフ8T6系など、機械式腕時計からアナログクオーツまで、さまざまな製品開発および生産設計に携わる。
外装設計
石田 正浩
2012年セイコーインスツル株式会社(SII)入社。ウオッチ事業部 商品技術部 設計グループにおいて、ライセンスブランドなどの外装設計を担当。2014年よりセイコーブランドの外装設計を手掛けている。
100年を超える伝統と技術から生まれた、新たな機械式腕時計
ムーブメント設計 平野 圭 |
外装設計 石田 正浩
インタビュー
1881年の創業以来、絶え間なく進化を続けてきたセイコー。1913年に発売した国産初の腕時計「ローレル」を皮切りに、さらなる高精度化、高品質化を目指して、次々と技術革新を図り、現在に続くジャパンメイドの機械式腕時計の礎を築いたエポックメイキングな発明の数々を世に生み出してきた。2018年、100有余年に渡るセイコーの機械式時計づくりの伝統とノウハウを受け継ぐメイド・イン・ジャパンの機械式ウオッチブランド「セイコー プレザージュ」の頂点を成すプレステージラインから新開発の薄型ムーブメント「キャリバー6L35」を搭載したモデル「SARA015」が誕生した。日本における機械式腕時計の変遷を辿るとともに、耐久性や視認性、使いやすさを保ちながら、薄型化を実現させた新たな機械式腕時計の開発の軌跡やこだわりについて知るべく、ムーブメント設計担当の平野圭と外装設計担当の石田正浩に話を聞いた。
2018年、新開発の薄型ムーブメント「キャリバー6L35」搭載モデルが誕生
2018年、新開発の薄型ムーブメント「キャリバー6L35」を搭載した「SARA015」が発表されました。開発のきっかけについて教えてください。
平野圭(以下、平野):機械式腕時計ならではの比較的重厚感のあるモデルだけでなく、今という時代のトレンドを踏まえて、「薄さを備えたエレガントなモデルも展開していきたい」という長年温めてきた企画を立ち上げるべくして開発がスタートしました。薄型の自動巻ムーブメントは自社では持ち合わせていないため、細部に至るまでの技術および製造革新が必要不可欠でした。当初、実現するにはかなりハードルが高いと感じていました。しかし通常、新製品開発には3~5年を要するところを、のちほどお話しする2つの要因からわずか2年の開発期間で、薄さを追求しながらも、実用性を十分に兼ね備えた腕時計を完成させることができました。「SARA015」に搭載した新開発のムーブメント「キャリバー6L35」は、現行の基幹ムーブメント「キャリバー6R15」と比較して、精度を高めながら、約1.3mmの薄型化を実現しています。
キャリバー6L35の開発において、どのような点にこだわりましたか?
平野:ムーブメントを薄くしたり、小さくすると、それを構成する各部品もおのずと薄く小さな“もの”になります。しかし、薄く、小さくすることは各部品の強度や剛性の低下を招くことになり、耐摩耗性などにおいては不利に働きます。例えるなら、手の甲を鉛筆の先で押すのと、削っていない鉛筆の後ろの部分で押すのとでは、同じ力であっても点と面の違いで手の甲への力のかかり方が違ってきます。歯車やレバーの噛み合いが多い機械式時計では部品同士が小さくなると、同じようなことが起きてくるのです。
ムーブメントの薄型化を図りながら、耐久性も確実に確保していく。キャリバー6L35の開発においては、これをクリアすることが重要なポイントでした。それぞれの部品の材料・硬度・仕上げを既存のムーブメントと比較し、何がベストなのかを試行錯誤しながら模索し続け、薄型化したムーブメントに如何に適合させていくかに力を注ぎました。
ムーブメントの設計は一人で担当されたのですか?
平野:キャリバー6L35の設計は、自身を含む三人体制のチームで行いました。ただ、三人だけで設計図をすべて作るというわけではありません。設計図が出来上がると、それを1~2週間かけて有識者3~4人が技術検証を行うステップが設けられています。ここで、改良するべき点などについてディスカッションを重ねながら調整を行い、皆で一つの図面と一つの機構を成り立たせていくという流れでした。
先述したように、通常、新しい機械式腕時計の開発には、3~5年の時間を要しますが、わずか2年で製品化を達成できたのは、次の二点が大きく関係していると思います。一つは、当社には機械式時計づくりにおける伝統と独自のノウハウがベースとしてあること。もう一つは、機械式腕時計やアナログクオーツ式時計など、異なる分野でのムーブメント開発で経験値を積んできた設計者がタッグを組んだことです。キャリバー6L35に限らず、当社では異なる経験値を持つ者同士が、互いの技術やアイデアを融合すべく交流を図り、良いところは取り入れ、どんどんブラッシュアップしながら、品質レベルを上げていき、さまざまなムーブメントを製品として立ち上げています。
例えば、同じ図面を見ても、機械式腕時計のムーブメント設計に長く携わってきた設計者と、アナログクオーツ式時計に長く携わってきた設計者とでは、着眼点が明らかに違います。機械式腕時計の観点では、構造が極めて複雑で、組み立てが非常に難しい設計であっても、ムーブメントの組み立てを手作業で行うことを前提とすれば、それを良しとすることが多いです。これに対し、アナログクオーツ式時計は如何にいいものを一度にたくさん作るかが大きなポイントになることから、ムーブメント自体の頑健性と組立の効率性を重視します。
アナログクオーツ式時計で豊富な経験を持つ設計者からのアドバイスは目からうろこの学びも多く、何より、製品の品質はおのずと向上していきます。しっかりとしたものづくりを行い、それを世に送り出していくための好循環なチームワークが築かれていると思います。
ムーブメント開発の過程で苦労したのはどんな点ですか?
平野:開発の話が持ち上がってからまだ日が浅い頃、企画者の要望に対して、設計上での具現化の目処がなかなか追いつかなかったこともあり、幾度となく議論を重ねたことがありました。企画者の目指す製品イメージは、時に設計者を苦しめるものになりますが、我々に限界を作らせずに、常にチャレンジさせていく気持ちを忘れさせないものにもなっています。
今まで我々の開発してきた中で、キャリバー6L35は自動巻メカニカルムーブメントとしては最薄です。現行の基幹ムーブメントに比べて精度を高めながら、薄さを実現するうえでは、やはり苦心しましたね。あとは耐久性の面でいうと、社内の基準をもとにした落下試験があるのですが、ムーブメントを構成している各部品とともに、それらを支える役割を持つ部材も薄く、小さくなっているため、衝撃で変形することにより中の部品が壊れてしまうこともありました。この点については、解析と評価を何度も繰り返すことで、セイコー プレザージュとしての頑健性を誇れるものとして仕上げていきました。
薄く、美しく、心地良く。外装に込められた珠玉の創意工夫
外装でこだわったのはどのような点ですか?
石田正浩(以下、石田): キャリバー6L35の薄さをより強調できる外装構造を、デザイン開発チームからの要望で開発しました。外装の薄さを強調しながら、心地良い装着感を兼ね備えたものであることも求められました。
裏ぶたとケース本体が一体になれば、全体としてより薄く見せることができるので、そういった構造を検討できないだろうか。当初、デザイン開発チームからは、そのような案も挙がっていたのですが、構造上の問題が一つありました。基本的に当社のモデルに関しては、オーバーホールを踏まえて、りゅうずを外すための極小の穴を裏ぶた側に配置する必要があるため、一体化することは断念しました。
代替案として、その小さな穴の部分のみを押せるハッチのようなものを付けてみてはどうかという声が挙がりましたが、設計条件に当てはめていくと、物理的に厚くなってしまうため、これも具現化するのは難しく、さらに案を練ることになりました。
そこで新たに出てきたのが、ベゼル側からダイヤルとムーブメントを投入するケース構造により、裏ぶたをコンパクトにすることで、装着した際に実際の厚さよりも薄く感じさせる外装設計です。この手法は、セイコーの高級品にのみ採用されてきたものであり、アフターサービスなど、中身を開ける必要のある時には、こじ開けと呼ばれる薄い板状の専用道具を使って、開けなければ外れない仕組みです。
むろん、万全の注意を払って作業にあたっていますが、SARA015 はセイコー プレザージュにおいて、これまでにない薄型化を図ったモデルゆえ、ガラス縁や胴に傷がつく可能性についても十分に検討しました。オーバーホールの際に繰り返しベゼルを取り外すことで、ベゼルと胴の双方にダメージを与えることのないよう、長期にわたるメンテナンスを考慮したうえで、最も傷つきにくく、何度開け閉めしても問題なく対応できる、世代メンテナンス性を考慮したねじ込み式のベゼルを採用するに至りました。
薄型化を図ったモデルならではの苦労した点について教えてください。
石田:先ほどの話の続きになりますが、ねじ式を採用することによって、おのずとねじを回すための溝が必要になってきます。構造上、それらは表に出てしまうため、美しく隠すために、飾り縁を上からかぶせた仕組みになっています。この構造によって基本的に傷つきづらくなり、ガラス縁とケース本体の間に「ステップ」という段差が生じることで、腕時計をサイドから見た時に横線が入っているように見え、さらに薄型化した印象を実現しています。これに関しては、デザイン開発チームの多大なる協力の元、実現することができました。
ご覧いただくと分かると思うのですが、SARA015の飾り縁は極めて薄く、繊細なパーツです。先ほども触れたように、メンテナンスの際に分解すると、変形してしまう恐れがあるため、全周に対して12時から6時側のみは少し飛び出るような構造とし、何度外しても変形せずにうまく外せる仕様となっています。さらにブレスレットが付くことで隙間がなくなるため、無理やりこじ開けたり、大きな衝撃を受けるなどしないかぎり、通常の使用環境では容易に外れない設計になっています。
機械式腕時計づくりにおける今後の展望についてお聞かせください。
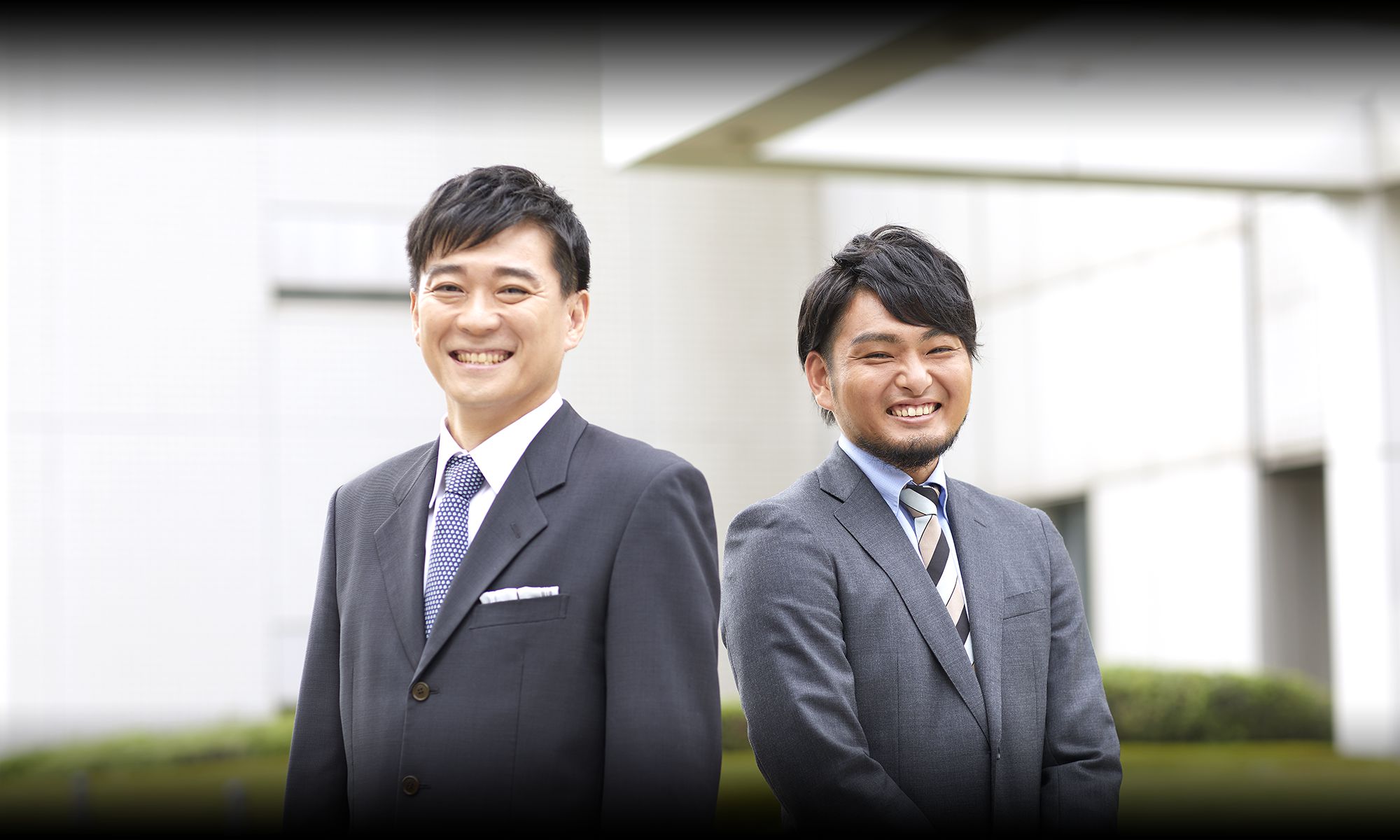